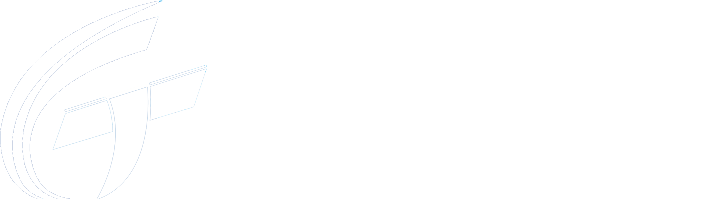
树脂砂铸造生产工艺流程
详情介绍:
一、 主要原材料的技术要求或规格
1.1、原砂(天然石英砂)
粒度:40/70目(中大件)或50/100目(一般件); 化学成分:sio2 >90% 、含泥量<0.2%~0.3% 、 含水量 <0.1~0.2%;微粉含量(140目筛以下) ≤0.5~1.0%、耗酸值<5ml 、灼减量<5、粒型:圆形或多角形。
1.2、再生砂
灼减量<3.0%;耗酸值<2.0ml;ph值<5 ;200目筛底盘<1%;底盘量<0.2%;含水量<0.2%; 粒形: 圆形。
1.3、呋喃树脂
含氮量2.0~5.0%;24h抗拉强度>1.5mpa;游离甲醛<0.3%;粘度<60mpa.s;密度1.15~1.25 g/cm3;游离酚<0.3%。
1.4、固化剂
采用有机磺酸固化剂,其黏度一般控制在<200mpa.s,水不溶物的含量<0.1%,同时冷冻和随后的溶解之间要有可逆性。为了保证稳定的型砂可使用时间和硬化速度,可选用“a+b”固化剂或根据季节不同选用不同酸度型号的固化剂。
1.5涂料
采用醇基涂料。要求涂料的固体含量高,粉料粒度细,粉料及黏结剂的耐火度高,抗爆热能力强等。具体工艺性能要求有:密度1.25~1.35 g/cm3;黏度6~7s;悬浮性(2h)>97%;涂刷性、流平性、渗透性、抗裂性要好,涂层强度要高。对于表面球化有深度要求的铸件,应采用氧化镁涂料。
二、操作工艺规程
2.1、再生砂准备
根据树脂砂再生设备的要求和工艺流程进行操作,获得满足工艺要求的再生砂。特别要注意控制好进入混砂机时的再生砂的温度,最好在25-35℃。
2.2、砂、树脂、固化剂加入量的调整
(1)混砂机的流量测定 根据混砂机的设定要求,在正常的生产情况下,至少每四天进行一次流量测定。分别对相同时间内砂、树脂、固化剂的流量进行称量,掌握时间流量。并先将砂流量按混砂机的公称流量进行调整。
(2)树脂量的调整 根据砂流量调整树脂的加入量,树脂加入量一般控制在型砂重量的0.8~1.2%,厚大件取上限,中小件取下限。
(3)固化剂量的调整 固化剂加入量在正常情况下与砂温和车间环境温度有关,一般控制在树脂加入量的30~50%,高温时取下限,低温时取上限。放砂时间长的大件固化剂加入量取下限,以保证树脂砂有足够的可使用时间。
(4)混砂机的调整与准备。
严格按《混砂机操作规程》进行设备的日常维护保养,特别是要及时清理搅笼内的叶片和内壁。每天放砂前应将树脂,固化剂泵单独循环1~2分钟,并注意检查固化剂加入孔是否有结晶堵塞现象。
2.3、模具整理与检查
①了解所生产铸件的工艺要求,熟悉工艺文件和工艺装备。
②检查模具芯盒是否齐全,清除模具芯盒表面存在的多余残留堆积物。
③检查模具芯盒是否存在缺角、变形,尺寸是否符合图纸要求;检查活块、浇冒口是否残缺。
④检查定位销、孔配合是否合适;模具的起模装置及吊运装置的安装是否合适。
⑤检查模底板是否平直,大小是否符合要求。金属平板的安装必须平整、四角垫平,并保证在一水平面上。木质底板的模具必须放在金属平板上造型,造型前应检查底板与金属平板结合面之间是否有杂物。
⑥砂箱大小是否合适,吊耳是否牢靠可用,大型砂箱是否有裂纹等缺陷。
⑦准备所需要烘烤的冷铁,芯撑(冷铁、芯撑烘烤后必须冷却至室温才能使用)起模吊运工具、通气绳、填砂的用的砂块。所用冷铁表面最好经过加工或毛坯表面无缺陷,一般厚大件冷铁使用不得超过3次,薄壁件不得超过5次。
⑧所有模具,芯盒均刷好脱模剂后使用。
2.4、加砂与舂实
①冷铁、活块、浇冒口模样,以及泥芯的出气必须根据工艺要求正确摆放。
②启动除尘器后开动混砂机,单搅笼混砂机应注意先去掉头砂后再进行放砂操作。
③中小件可以从模样上放砂,放砂时应注意防止冷铁和活块的移动,并注意拐角、凹槽部位用木棒捣实,其他部位也得用木棒均匀捣实,特别要防止靠近模样部位的型砂局部松散。
④大型铸件应从砂箱某一角开始放砂,并注意适当调整固化剂的加入量,延长树脂砂的可使用时间。要边放砂边捣实,从砂箱一角逐渐沿模具其它方向连续扩展,直至放满整个砂箱。对于大空间砂箱,树脂砂可随模样形状放置一定厚度,一般控制在150~200mm (不填砂块情况下),必须保证浇口、冒口、出气孔部位的树脂砂达到工艺要求的高度,浇冒口、出气孔部位的高度可用冒口圈等达到工艺要求。
⑤放砂结束时,应注意尾砂不得放在浇冒口、出气孔部位,只能放在不重要的地方。
⑥由于树脂砂的流动性非常好,舂实只要求速度快,但不必过分用力。拐角、凹槽等部位必须要舂实。
⑦待砂放满后,刮平砂箱和芯盒并气针扎气孔。对于厚大件、墙板件等在盖箱上造型时必须认真扎好通气孔,并控制离模样30~50mm的距离,不能扎透。
2.5、起模
①几分钟后树脂砂略有变色发黏,可拔出冒口、直浇口、出气棒等。
②起模时间的确定。当砂型外层硬化,内层有强度但未完全硬化时起模。起模时间控制的好,有利于保护模样和加快砂型硬化。起模时间太早要塌箱;太迟,起模困难,容易损坏模样。一般认为树脂砂可使用时间与脱模时间之比为0.3~0.5。目前暂定可使用时间为7~15分钟,脱模时间设定为20~45分钟。起模前要检查确认砂型达到足够的强度,可用手在冒口定位等凹进部位触压测定,根据经验及模型实际情况确定,并注意实际起模时间在冬天、夏天,木模与金属模不同时均有区别。
③型板模造型的起模要求:检查吊链是否牢靠,长度是否合适; 起模时应调整好天平吊与型砂的重心位置,无法调整的应予以配重;先点动行车起模,确认分型面与模板平行后方可起模; 当砂型离开模样后应迅速起模;起模方向应垂直于模板;起模时平板不能吊的太高,移动时必须注意使平板平行下落。
④实样模的起模要求:a树脂砂达到起模强度后翻箱,准备起模;b将起模吊环拧紧到起模螺丝上,并将链条穿入吊环,并调整合适的长度;c调整行车到合适的位置,将链条拉紧并微调链条的长度;d用橡皮锤边敲打边起模,起模动作先缓慢,当模样快出砂型时应快速上升;e起模方向应垂直于分型面,并通过模样重心;f模型起出后,应将模样擦净,并将活动的浇冒口、模样等放在指定的地方,避免损坏、丢失。
⑤起模后砂型放置
起模后的砂型应放在一个指定的地方。下面四角须垫实(对强度不高的砂箱特别注意)、下箱要放水平,观察分型面是否平整,若不水平须调整下面的垫块。
2.6、修型
起模后需要对起模后破损的部位进行修补。具体要求如下:
①因起模而带断的凹槽、拐角或棱角处的破落砂块,如果整块未破碎,只需吹尽断裂部位的浮砂粒,用粘补胶重新粘住即可,在后序刷涂料时将其缝隙用涂料填塞。
②如果破损处的砂块已经碎了,可用新混的树脂砂修补。修补前做出倒钩槽(或将破损处挖大些),插上钉子,并吹净浮砂粒,再用新混的树脂砂进行修补。硬化后将多余的部分用砂轮磨去。
③砂型破损小或局部砂型疏松有孔洞时,可用稠厚的涂料浆修补。修补时刮刀要用力将涂料压入孔洞中。
④破损处型砂强度的检查,可用手用力擦试,以铸型表面不会落砂即可。
2.7、刷涂料
刷涂料是树脂砂造型过程的关键环节,直接影响着铸件的表面质量.
①刷涂料前应将涂料桶内涂料搅拌均匀,并用酒精调整到合适的浓度。
②对于大件应集中从某一部位刷起,涂刷速度要快且均匀,不得有流痕和刷痕。必要时可用酒精将流痕和刷痕清洗掉,涂刷完毕后应迅速点燃。
③涂料层厚度一般掌握在0.3~0.5mm,薄壁件取下限,厚大件取上限。浇注系统和冷铁部位涂料厚度取上限。对表面质量要求较高的铸件,最好刷两遍涂料,最后用酒精刷一遍。批量较大的件可采用流涂的方法上涂料,以提高生产效率。
④涂料刷毕后根据客户对铸件表面质量的要求不同,可采用软绸布对涂料层进行打磨,去掉微小的流痕和刷痕。
⑤应注意泥芯头和芯座不能刷涂料,并防止通气孔被涂料堵塞。
⑥应检查涂刷后的铸型表面质量,有无涂料堆积,如有可用工具铲刮掉。
三、制芯应注意的要点
3.1、芯骨的准备
①检查芯骨强度是否足够。
②芯骨放入芯盒,检查大小是否合适,吃砂量是否足够。
③用钢管做的芯骨,钢管上要有足够多排气孔,并适当绕一些通气绳。
④用铸铁做芯骨,芯骨上应绕足够多的通气绳,以加强泥芯的排气。
⑤检查芯骨用于起芯吊运砂芯的吊环是否可靠。
3.2、制芯操作要点
①整体式芯盒
在芯盒内放入以缠绕通气绳的芯骨,调整各部分至合理的吃砂量,将通气绳引出芯头。将芯骨的吊环整理好,露出舂砂面。芯骨应低于舂砂面一定厚度,此厚度随砂芯的大小不同而不同。放砂并舂实,砂放满后刮平芯盒。砂芯固化一段时间并达到足够强度后起芯。起芯时应找准砂芯的重心,行车点动起芯,并用橡皮锤敲动芯盒,当砂芯脱离后应快速起芯。砂芯起出后应放在松软的砂袋上,并垫平,防止砂芯变形。
②分体式芯盒
a 把芯盒清理干净,把两半芯盒夹紧。
b 放入绕有足够通气绳的芯骨,芯骨的吊环露出舂砂面,通气绳露出芯头。
放砂并舂实,砂放满后刮平。
当砂芯达到足够强度后,打开芯盒夹紧装置,打开两半芯盒。取出砂芯,放置在松软的砂袋上,并垫平,防止砂芯变形。
对于特殊形状泥芯,垂直舂完达到足够强度后可连同芯盒整体放置水平,打开夹紧装置,取出泥芯。
③脱落式芯盒
脱落式芯盒主要用于结构较复杂或拔模斜度小的砂芯,脱落式芯盒与上面两种芯盒方法不同是:当砂芯达到足够的强度后打开芯盒夹紧装置或外框,分别取出活块,吊出砂芯。
3.3、砂芯检查
对于复杂或重要的砂芯,制成后应用样板或专用量规进行尺寸、形状、表面质量检查。
3.4、配模
3.4.1、空合箱检查
对于首件、首批或重要的较大铸件,为确保质量,下芯前必须进行空合箱。空合箱时,将长的箱销插入盖箱销套内,下面伸出部分以不超过120mm为宜,用行车借正砂箱位置(销子孔对准),不能用人拉,注意此时下箱平面的距离四周应基本一致(否则应调整),合箱速度要慢。合箱后,仔细观察型腔情况,是否有错位及上下箱平面结合不平等情况,确认符合要求后在上下箱分型面做三道视线,便于检查,若空合箱时发现情况,应及时与技术人员联系,确定解决方法。
3.4.2、下芯
1)下芯必须熟悉铸造工艺图和工艺要求,了解铸件的基本结构、砂箱间及砂芯与砂型的相对位置、砂型数量等,防止下芯位置和方向发生错误或漏放砂芯。
2)根据工艺图的要求,确定下芯次序,以提高铸型装配精度。
3)检查砂芯质量
①不得使用破损、返潮、表面粉化或放置时间过长的砂芯。
②修补过的砂芯应作表面加固,待彻底固化后才能使用。
③芯头过大的砂芯应对芯头作适当修削后才能下到砂型中。
④芯头尺寸过小的砂芯下芯后应采用树脂砂或其他堵塞材料对芯头与芯头座的间隙作适当填补。
⑤检查砂芯的排气通道是否畅通。
4)准备干燥的芯撑、下芯工具及下芯后砂芯检验样板或量具。
5)组装砂芯:复杂的砂芯常需将几个砂芯预先组装后再下到砂型中,下芯前应检查组装砂芯的相对位置是否正确,砂芯间接合是否牢固,分芯面是否合适。
6)下芯操作:
①采用下芯夹具,将砂芯在定位装置导引下下入型腔。
②手工下芯时应注意:a 吊装砂芯确保通过砂芯平面重心;b 砂芯应平行于下芯片面; c 手扶砂芯确保砂芯稳定。
7)下芯后检查
①下芯后立即检查的项目有砂芯位置和数量、砂芯与砂箱相对尺寸、砂芯间相对位置。对弯头等圆形铸件应检查砂芯的分型面与砂型的分型面是否平齐,不平齐应做相应调整。
②填塞芯头与芯座,疏通砂芯排气通道。
3.5合箱
3.5.1、合箱前的准备
①熟悉铸造工艺,了解铸型结构特点,准备好型芯撑,过滤网、浇口杯、冒口所需的砂芯等。
②检查型腔和砂芯的芯头的集合形状和尺寸,损坏的要修补或更新,修补的砂芯要进一步检查,让其他完全固化,并刷好涂料。
③清除型腔、浇注系统和砂芯表面的浮砂和脏物,检查出气孔和砂芯排气通道,保证畅通。
④砂芯在砂型中装配后检查其形状、尺寸和间隙,符合要求后紧固砂芯。
3.5.2合箱操作要点
①铸型的分型面上要清理干净,沿分型面、芯头及气孔周围垫上封箱胶或封箱泥条。
②翻转上箱时要注意安全,翻箱后砂型有损坏要进行修补。
③检查上箱气道是否通畅,冒口、浇口内壁是否干净,检查上下型的定位部分是否准确无误。
④合箱时上箱要呈水平状态,缓慢下落,准确定位合箱,如分型面处要芯撑,则要用黄泥确定芯撑高度,再放合适的芯撑,然后水平地合上上箱。
⑤对大型铸件合箱前应进行空合箱。合箱应检查标记线是否对正,若偏差,应找出原因。若不能解决则坚决不予浇注,并重新开箱查找原因。
⑥检查直浇道与横浇道位置,砂芯有无卡砂的可能。
⑦检查分型面处是否合严,如有间隙应用耐火泥封箱,杜绝跑火。
⑧计算抬箱力,根据抬箱力放好压铁或选择紧固螺丝紧固铸型。
⑨放浇冒口杯,盖好浇口杯,准备浇注。
⑩所有的出气孔处要留有标记,以便点火引气,冒口要盖好,防止异物掉入。
3.6浇注
3.6.1浇注前准备:
①熟悉所浇注铸件的结构和浇注系统,并应知道所浇注铸件所需铁水重量。
②熟悉浇注铸件所需要的浇注时间,须在规定时间内浇完。
③清理浇注场地,保证浇注场地畅通无阻。
④在所浇注铸件砂箱周围垫一层薄砂。
⑤确认浇注杯是否正确安放,砂箱是否封好,紧固螺丝有无松动或压箱铁是否足够。
⑥摆放好浇注台架,并确认安全不晃动。
3.6.2浇注
①除净金属液表面熔渣,用茶壶包浇注,除净茶壶嘴熔渣。
②浇注小件或浇注时间长时可在金属液上洒上层稻草灰或珍珠岩保温。
③浇时不能中断,始终使浇口杯充满,在铸件工艺流程卡上规定时间浇完。
④浇注开始时应该以细流金属液浇入,防止金属液飞溅,待快浇满时也应该以细流金属液浇入,防止金属液溢出和减少抬箱力。
⑤铁水温度须达到工艺卡规定的浇注温度,低于浇注温度的金属液不能浇入铸型。
⑥浇注时在砂型出气孔和冒口处引火燃烧,使铸型中产生的气体易于及时排出。
3.7、铸件的冷却时间
3.7.1为防止铸件在浇注后因冷却过快而产生、裂纹等缺陷,并保证铸件在清砂时有足够的强度和韧性,铸件在型内应有足够的冷却时间。
中小型铸铁件在砂型中的冷却时间
壁薄重量轻的铸件冷却时间取下限值,反之取上限值。
3.7.2、大型铸铁件的冷却时间
计算大型铸铁件型内冷却时间的经验公式:t=K*G
式中:t—铸件冷却时间(h)
K—铸件冷却速度4~8(h/t)
G—铸件重量
3.8、应注意的几个问题
1)树脂砂必须保持洁净,不得混入其他种类的型砂或其他夹杂物。造型过程中要注意不能将废弃的封箱用耐火泥、陶瓷片等杂物混入型砂,以免增加灰分。
2)树脂与固化剂桶必须严格区分。由于树脂和固化剂混合后将产生剧烈放热反应,严重时容易产生爆炸,因此必须严格区分和隔离。
3)树脂、固化剂涂料均系易燃易爆物品,树脂砂生产场地应严禁吸烟。
4)定期定量补充新砂。在树脂砂的再生过程中,将产生的5~10%的微粉并被除尘器除去,因此至少每天应均匀补充5~10%的新砂,以确保砂量的平衡。
5)树脂砂用原砂和再生砂应严禁受潮,一般对树脂砂来讲水份超过0.2%就会影响固化,
甚至造成不固化。
6)树脂砂生产过程中一定要掌握好树脂砂的可使用时间,超过可使用时间的树脂砂严禁使用,以免影响砂型或砂芯强度。
7)混砂机应定时清理,除净叶片上的附属物,并调整的搅笼内叶片的角度,确保混砂质量。
8)树脂泵和固化剂泵应经常清洗,确保流量正常。
9)定期测试砂流量、灼烧减量、型砂抗拉强度等。
10)定人定期清除灰分。
11)定人定期检查维修、保养再生系统、除尘供风系统。
四、检验和记录
树脂砂生产过程中的检验和记录按照公司有关规定执行
五、树脂砂造型对模具工艺的要求(树脂砂生产线):
与粘土砂相比,树脂砂铸件的外观质量依赖于模具的质量,因而树脂砂对模具的质量要求较高。模具工艺时使其较好的适应树脂砂造型的需要,主要在以下几个方面:
加工余量:硬化后的树脂砂铸型有较好的刚度和较高的尺寸精度,且不易变形,所以在选择工艺参数时,可以选取较小的机械加工余量,从而减少金属溶液的消耗和机械加工的成本,从而可以提高铸件的尺寸精度。
拔模斜度:树脂砂在起模时已具有一定的硬化强度,较小的退让性,较大的摩擦力,若采用敲击的方法起模,容易损坏模具,同时树脂砂的可修补性差,起模时,若受到破坏,较难修补。采用树脂砂造型时,应根据生产实际和产品结构加大模具的拔模斜度,能顺利的起模,得到质量随着市场对铸件产品外观质量要求的不断提高,树脂砂铸件在品质上的优势,必将日益受到重视,树脂砂这一铸件生产工艺,也必将得到迅速的发展和普及。
模具的表面粗糙度:模具表面的粗糙度对树脂砂铸件的表面粗糙度起决定性的作用,因而尽量降低模具表面粗糙度,是获得高品质铸件的重要措施.
Copyright © 江苏高群节能科技有限公司 2021.All right reserved.Powered by 江苏高群节能科技有限公司 苏ICP备2022021011号-1